New CAE dimension is convincing
Dressel GmbH in Unna has been amongst the EPLAN Electric P8 users from the very beginning.
Dressel GmbH in Unna, Germany, a renowned provider of electrical-engineering and automation solutions for demanding industrial applications has been amongst the EPLAN Electric P8 users from the very beginning. The conclusion of the electrical engineers: The higher the demands made by the customer, the faster EPLAN Electric P8 pays its way and the better one can react to customer requirements. When electrical equipping of automated plants is required, Dressel GmbH has an excellent reputation in various branches of mechanical and plant engineering – from wind energy through sheet-metal and tube forming to press technology. The company, founded more than 20 years ago and employing more than 70 persons, concentrates on demanding tasks in control and automation engineering. Authorized officer Dirk Fischer: "In most cases we take over the complete added value chain from planning the complete electrical-engineering and automation technology through enclosure manufacturing to commissioning the plant on site". And the standards they set themselves are high – with the consequence that customer loyalty is high and the project planning team is also familiar with difficult tasks such as modernizing the control-engineering system of existing plants.
Example: Manufacturing plant for sandwich elements
A current example of a typical project is a plant for manufacturing noise suppression plates with an intermediate layer made of polyurethane foam. These plates with a length of up to 16 meters are used to clad roofs or walls of buildings and since they are manufactured exactly to the dimensions specified by the architect, the plant with a length of more than 200 meters has to be correspondingly flexible. The sheet coils are first profiled. In the next step the foam is applied to the lower sheet and then the upper sheet to the foam (whose thickness can differ depending on the insulation effect required). After the elements have hardened and cooled down, a flying saw cuts the parts to measure. At the plant outlet a conveyor then stacks the cut elements sorted by the relevant commission and ties them up or packs them in films.
Flexible automation
The "highlight" is the flexibility with which the sandwich plant cuts sheets and commissions them: The cutting sequence does not have to be commission-specific and the stacking is also not necessarily carried out in the order of production. An ingenious control technology is required to this purpose: The master computer communicates with the individual control systems, the visualization systems on the basis of a PC control system and the client computers by Ethernet. The complexity of the process is indicated by the fact that sixty enclosures and a central control center are installed along the plant.
More than 20 years of EPLAN experience
Anyone who has to master such complex task requirements in a short period while setting themselves high standards requires powerful tools in addition to competent and experiences project engineers. The Dressel project engineers have been working with EPLAN for more than 20 years. After extensive experience with EPLAN 5 – that is still used when desired by a customer – the company was one of the first to use EPLAN Electric P8 for their electrical engineering. And there's more: Dressel belonged to the alpha and beta testers of the new platform and, with Bernd Gischel, has managed to win over a well-known CAD expert who not only moderates the EPLAN forum on the www.cad.de website, but has also written specialist literature on the topic.
From drawing to designing
At Dressel one is convinced of the new platform. Bernd Gischel: "With EPLAN 5 one primarily drew. Now one can use a completely different approach and work object-oriented by, for example, starting from the field devices." A further advantage in his opinion is the automization of many recurrent steps - bringing not only savings in time: "This approach also allows errors to be avoided. For example, the contact assignment of contactors can be stored as a function template."
Documentation simplified tangibly
As alpha and beta testers Dressel were able to familiarize themselves comprehensively and early with the new platform – in view of the numerous additional functionalities an advantage that is not to be underestimated. Bernd Gischel: "EPLAN Electric P8 offers many functions that were not possible at all in EPLAN 5:" It therefore pays off to convince customers with whom one exchanges data to change over. But the customers also notice that electrical engineering with EPLAN Electric P8 is more powerful: "The documentation can be structured much more simply and precisely in accordance with the customer's requirements. For example, it is very easy to generate lists of the used parts - the planning procedure has once again been structured even better through the new software."
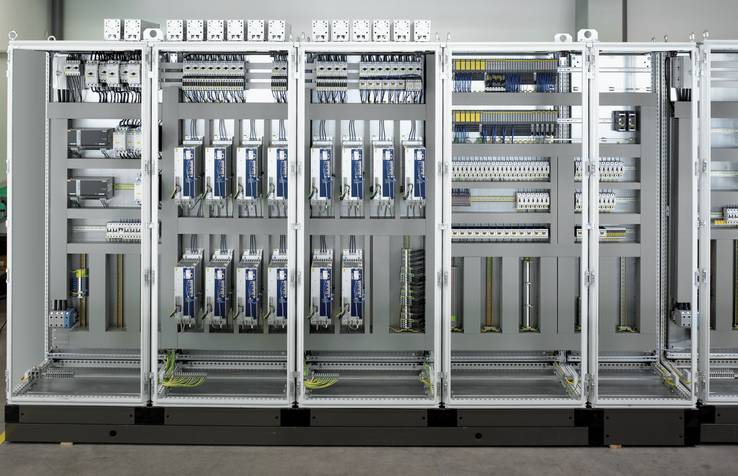
Complex projects with 60 and more enclosure fields also belong to the day-to-day business of Dressel – a powerful and versatile tool for electrical design becomes increasingly important.
Clear procedures
Dressel works with six P8 licenses and has invested a lot of time in an optimal rights management structure – it should not be possible for every designer to do everything. Designing is carried out completely in EPLAN Electric P8 until at the end the complete bill of materials is transferred to the EPLAN PMS production planning and control system. Bernd Gischel: "EPLAN PMS is actually no longer required for EPLAN Electric P8, but since some of our customers still want us to work with EPLAN 5, we will be keeping this proven system for the time being." This is also due to the fact that the electrical engineering and the PPS system are well attuned to each other at Dressel. Not only the used components are recorded project-specifically in EPLAN PMS, but also the time that each employee invests in the project: an optimal foundation for realistic costing.
Good coordination between hardware design and software development
The new platform also provides a good foundation for coordination between the various trades. Bernd Gischel: "In the initial design phase intensive discussions take place between the colleagues in electrical engineering design and the software development and programming, who are in part involved in the device selection or specify the bus system to be used."
Electrical design for demanding markets
The Dressel engineers use these procedures not only to develop plants for metal machining with EPLAN Electric P8, but also other demanding projects. Authorized officer Dirk Fischer: "A further working field in which we have an extensive know-how is, for example, wheelset presses for tail technology. In this case the integration of the sensor equipment plays an important role. Just as complex are the plants for tube forming which, for example, wind serpentine tubes from coils: High demands are placed on the welding technology in this case. In the field of logistics we have implemented interesting projects such as in modernizing high-bay warehouses in which existing hardware is equipped with a new control technology system."
Standardized systems for wind energy technology
The wind energy market has developed to be a very important market for Dressel. Dirk Fischer: "Our automation technology is installed in almost all the large wind energy plants with outputs of several megawatts. As a rule we supply six to seven enclosures per system, including for the pitch regulation." In contrast to other markets, these systems that are produced on a separate production line at Dressel are standardized to a great extent, meaning that the amount of engineering involved is low.
Using all possibilities
On the other hand, the effort required for the documentation is comparatively high, so that using EPLAN Electric P8 would be of great advantage. Dressel is therefore planning to also integrate the enclosures for wind energy systems in P8. Bernd Gischel: "However, we not only want to import the data, but rather virtually design the systems again in EPLAN Electric P8 in order to exploit all the possibilities provided by the new software. We can then store many more data. This gives us the option to adapt the documentation flexibly to the individual requirements of our customers." This work has to be done parallel to the day-to-day business and at Dressel all the project engineers are already fully occupied. Nevertheless those responsible are convinced that the work will pay off, since EPLAN Electric P8 improves the documentation considerably and the customers appreciate the result.