Electrical engineering at Hahn Automation Group
Millimetre Accuracy: Cable routing for specialised plant systems
Hahn Automation Group is following a clear concept for the further development of its electrical engineering. After rolling out EPLAN Pro Panel, the company is now one of the first (test) users of the EPLAN Cable proD cabling tool. The 3D cable routing on complex and highly automated specialised plant systems has resulted in cost savings and increased overall quality – and even their service and maintenance technicians are benefitting from precisely preassembled cable harnesses.

The company headquarters and its largest manufacturing facility are located in Rheinböllen, Germany, home to about 650 of the company’s 1,800 employees. (© Hahn Automation)
Curved or in a portrait format, with two or three sections or even across the full width of the windscreen: displays are the visualisation and control element in the driver’s cockpit. Automobile manufacturers and their suppliers are constantly coming up with new ideas for this very flexible human-vehicle interface. Effective and efficient manufacturers of plant systems for highly automated manufacturing are laying the groundwork to ensure that the new generation of such displays can be mass produced in the highest quality. Hahn Automation Group is at the forefront of this demanding field.
At the company’s headquarters in Rheinböllen, in southwestern Germany (as well as at other facilities around the world affiliated with the group of companies), there are a wide variety of systems for the automated manufacturing of complex components used in production or testing – not just parts for vehicle interiors. Hahn Automation Group systems also produce sophisticated components for electronics and for medical technology – from pipettes to pacemakers. All are characterised by a high degree of automation and short cycle times – and each system is unique unto itself.
Electrical engineering right from the start
No matter the size of the plant system or the target industry, the company’s electrical engineering designers have been relying on EPLAN for around fifteen years. Electrical Engineering Manager Dirk Scherer says: “We create the schematics using EPLAN Electric P8 and send the generated bills of materials and I/O lists to the procurement and manufacturing departments.” The company has been using EPLAN Pro Panel to design the control cabinets for a good two years now: “This doesn’t just speed up control cabinet production, it also increases their quality – thanks to the 3D visualisation alone.”
Foundation: In-house device database
The foundation for the electrical engineering designs at all the group’s worldwide locations is a uniform device database that is continually being updated. Two to three employees are involved in this task: they enter new devices and enhance the datasets to ensure that the quality of the data remains both high and consistent. This in-house device database uses the EPLAN Data Portal as its basis, and the design engineers can often find and make use of existing devices, not to mention existing macros.
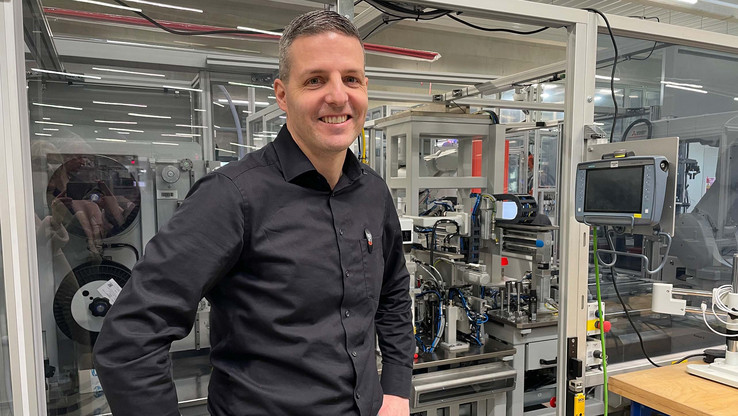
Hahn Automation Group manufactures complex, highly automated systems – including for the assembly of displays for vehicle cockpits. (© EPLAN)
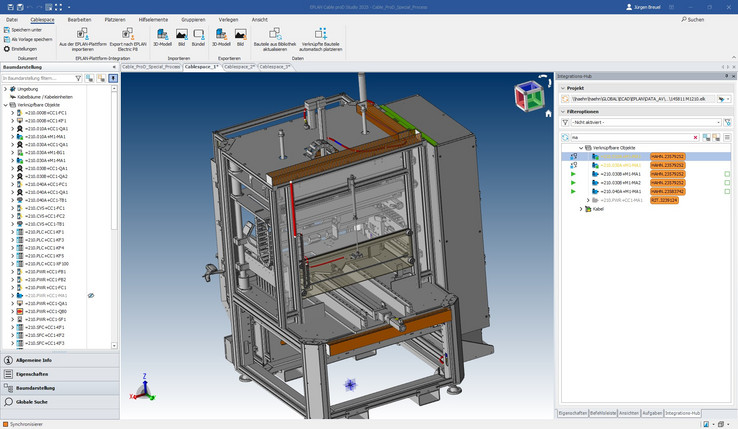
Based on the schematics and MCAD data, EPLAN Cable proD is used to determine the cable lengths and routing pathways for installation. The exact cable lengths are then fed back into EPLAN Project. (© Hahn Automation)
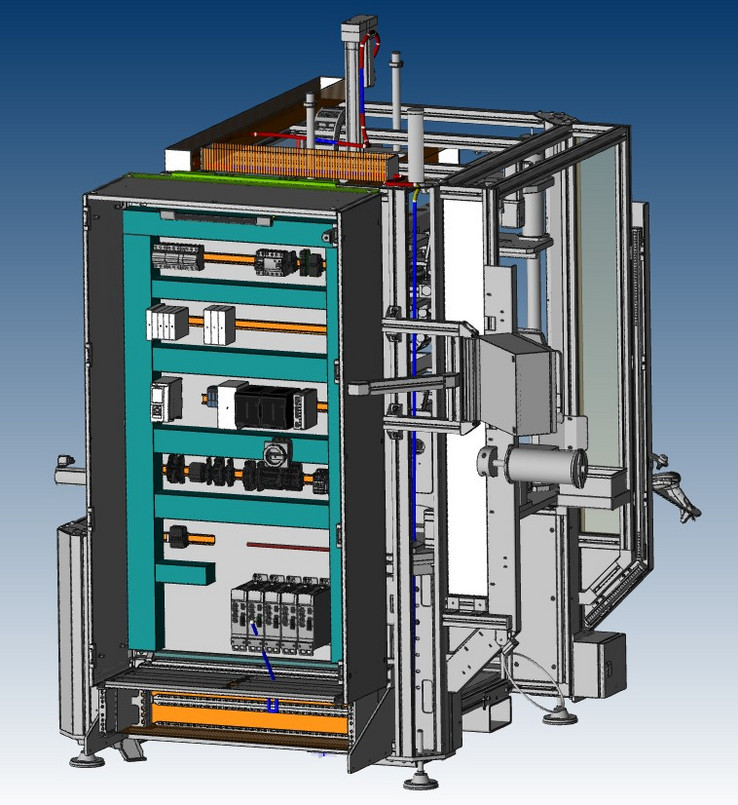
EPLAN Cable proD precisely determines the cable lengths based on the control cabinet layout from EPLAN Pro Panel. The 3D routing of the cables in highly automated customised plant systems saves costs and increases the quality of the final product. (© Hahn Automation)
Project: The future of control cabinet production – machines that do the cabling
Two years ago, with the introduction of EPLAN Pro Panel, the company managers developed a concept for advancing in-house control cabinet production, which takes place at the facilities in Rheinböllen, Germany, and Sveta Nedelja, Croatia. The concept also dealt with an area outside of the control cabinet: laying cables on the plant systems themselves. Dirk Scherer: “We lay a large number of cables for each plant system, including expensive servo cables. If the lengths of these have only been approximated, either extra cable goes to waste or sometimes a cable is too short. And the installation routes for the cables can be random and may not end up being optimal. We wanted to standardise this and make the process more efficient.”
Machine cabling in practice – beta testing Cable proD
So it was a good thing that EPLAN was planning the market launch of just the right tool for precisely this task: Cable proD. This CAD tool can lay cables virtually in the field and automatically determines both the required cable length and the exact installation routing – based on the schematics from the MCAD data. The exact lengths are then fed back into the EPLAN Project.
Hahn Automation Group agreed with EPLAN to test Cable proD on the specific example of a system for the automated production of automotive components with a cycle time of 41 seconds. Eighteen workstations here must be supplied with power and signals, and because some of the work steps are complex (including cold shrinking with liquid nitrogen, for example), around three hundred sensor cables, fifty power cables and eleven servo cables had to be laid.
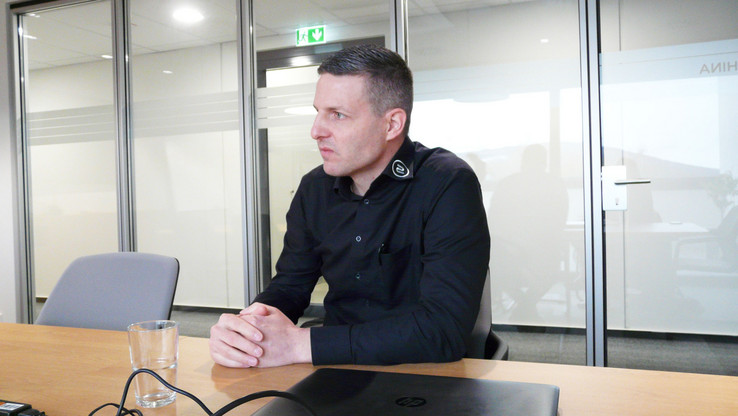
Hahn Automation Group Electrical Design Manager Dirk Scherer (© EPLAN)
The results: “Right the first time” instead of “Wrong again and again”
The test results thoroughly convinced Hahn Automation Group. Dirk Scherer: “The cables are bundled and routed through cable channels in 3D. The system reliably determines the cable lengths, so you don’t have to measure beforehand or make corrections after the fact. And our technicians can work quickly without making any mistakes because the routing paths are displayed in the viewer.” Another advantage is that the expensive servo cables can be produced without any waste, saving money and copper, and doing it all with lower overall carbon dioxide emissions.
Improved service as well
Hahn Automation Group also sees improvements at yet another level – for service and maintenance. Dirk Scherer: “Many of the cables in our systems are in constant motion and are therefore subject to wear and tear. That means that our clients order replacement cables that we have to replicate. When the exact length of those cables is already recorded, we can produce a perfectly fitting cable set and offer the client quick service with the exact cable or cables they need.” This naturally also holds true for cables for the energy chain – and also when a replacement set is required for a new product or a new tool. The cables can be manufactured to the same standards as the existing ones.
Outlook: Moving from drawing to configuring
Following its successful test, Hahn Automation Group has decided to first introduce EPLAN Cable proD at its facilities in Rheinböllen and will then roll it out to its other locations. This makes sense for the long term as well, as automated cable routing is a good fit for the future of plant system manufacturing and control cabinet production. Dirk Scherer: “We are certain that we will no longer be drawing schematics, but configuring them. We have already completed the groundwork for this, such as the device database, the macro project and the basic project. Power requirements and climate-control needs can already be automatically created right now. This will continue to make us even more efficient and enable us to increase our focus on innovative design.”

Hahn Automation Group plant systems are characterised by their high performance and compact dimensions – here is an illustration of a system for the automotive sector, including its digital twin. (© Bild Hahn Automation)
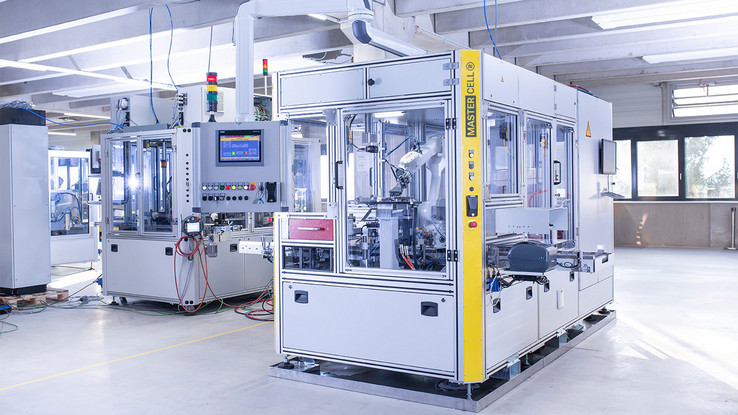
Mastercell robot arm with gripper (© Hahn Automation)