High-precision modular innovative mechanical engineering
Using the platform-based design tools EPLAN Electric P8 and EPLAN Fluid, they have successfully developed highly efficient modular transfer centres with the precision and productivity formerly associated with specialist machines.
The developers of machine tools for the automotive industry at the Krause & Mauser Group turned the normal process logic in turning/milling centres on its head in its PS INVERS3 by moving the workpiece instead of the tool. Using the platform-based design tools EPLAN Electric P8 and EPLAN Fluid, they have successfully developed highly efficient modular transfer centres with the precision and productivity formerly associated with specialist machines.Nothing is set in stone. Not even the workings of NC machining stations. So who says that the workpiece has to stand still and the machining spindles and tools have to move? Wouldn't the reverse procedure have significant benefits? Extremely short span-to-span times can be achieved by eliminating tool change times and tool change error. It also allows the machining of a wide range of workpieces from one multiple-spindle machining process to the next based on a multiple spindle arrangement on up to four sides and gives shorter throughput times than a transfer machine. The patented spatial frame construction provides an unprecedented level of stability. At the same time, the machine provides exactly the level of flexibility required for the production of automotive parts. The modular approach makes it possible to comply with modern production philosophies, including staggered investment, parallel roll-out and discontinuation of product ranges.PS INVERS3 - more productive, more precise, more profitableIn its hybrid processing module PS INVERS3, the Krause & Mauser Group combines the flexibility of a machining centre with the productivity and precision of a specialist machine. This highly productive yet modular production concept moves and positions the pinole-guided workpiece against the replaceable spindle heads arranged on up to four sides of the machining area. If necessary, these can be replaced completely instead of changing the tools individually. This means the PS INVERS3 can be used to machine a wide range of workpieces, without compromising on precision or production efficiency. A wide range of different technologies, including milling and drilling and also smoothing or honing, can be integrated, which means that complete machining is often possible without replacing the tools.At the same time, if used as a bed for the travel axles and a holder for the multiple spindle heads, it is an extremely compact sealed frame construction of which the static components and those which have an influence on the process can be consistently water-cooled. Fluid integration and changing standardsThe electrical engineering element of the PS INVERS3 was designed on EPLAN Version 5.70. This was also used to create the plans for the hydraulic and pneumatic elements of the machine tools. But Ing. Manfred Haslinger, Project Manager for Electrical Hardware at Krauseco, remembers that "the documentation was very much a compromise. It used various cross-reference functions and was really just a graphical representation."The launch in 2008 of EPLAN Electric P8 and the EPLAN Platform, which allow the incorporation of other development tools within the same workflow to produce consistent documentation, was a good reason for the developers in the two Krause & Mauser factories to seriously contemplate the option of integrating electrical and fluid planning. "These efforts were supported by considerable internal pressure to switch over to EN 81346," explains Dipl.-Ing Mihaly Sütöri, Head of Electrical Configuration. The standard describes structuring principles and reference labelling for industrial systems, plant, equipment and industrial products, and represents the document guidelines recognised by the customer.Incremental data migrationThe switchover of the design system for electrical and fluid power design followed a short yet intensive selection and evaluation phase. "By comparing different software products directly, we were convinced that EPLAN had made an important move in switching over to a database system," reports Manfred Haslinger. Since early 2010, the electrical engineering parts of the plants have been developed on 11 workstations running database-assisted EPLAN Electric P8, with the pneumatic and hydraulic components developed using four EPLAN Fluid licences. "We were happy to undertake the work involved in the move to improve the master data in order to exploit the benefits of EPLAN Electric P8 and the platform as effectively as possible."Despite the huge amount of old data, this additional workload was manageable and did not become stressful. All the parts data was initially taken over from the existing system unchanged. Additional details were gradually added when they were first used in new systems, the documentation for which typically consisted of around 500 pages of electrical plans and 100 pages of fluid plans and enclosure plans. This incremental data migration was also often used to replace outmoded plant parts and assemblies with more modern and economical solutions.Benefit of modularisation"The investment of valuable working time into the creation of a database with improved data quality quickly paid off," Manfred Haslinger is convinced. "The consistency of development and documentation of all electrical, pneumatic and hydraulic systems alone is noticeable thanks to the elimination of notorious error sources at the interfaces and thus the reduced commissioning costs." Added to this is the increased consistency of the texts and translations, the acceleration of the document creation process with the option of working based on either graphic or object-orientation, and additional features to make further data processing easier, including exporting to external programs. The document creation process is also made quicker by the fact that less work is required on checking and manual corrections. Virtually unlimited options in terms of configuration, documentation and management of projects support interdisciplinary work. Data from previous planning phases can also be easily adopted via interfaces such as ODBC, XML and Excel. "We are coming across more and more areas in which EPLAN Electric P8 and EPLAN Fluid offer increased efficiency and productivity," explains Mihaly Sütöri, indicating that the switchover was still a work in progress. "Even now, we are benefitting more than anticipated from the considerably simplified design process for reusable modules for the development of variants and options which EPLAN Electric P8 offers."Enclosure construction includedKrause & Mauser has outsourced enclosure construction to a leading manufacturer in Germany. "With the switch to the new versions of EPLAN, it is now very easy to operate the interfaces to production," explains Mihaly Sütöri, who is pleased about the increased efficiency at this point. "This not only affects the data for the electrical switchgear design, but also, for example, the signage for the hydraulic and pneumatic systems." In future, the data from Vienna and Oberndorf will be sent directly to the wire fabrication machine owned by the panel layout engineers, which will reduce time-to-market even further.
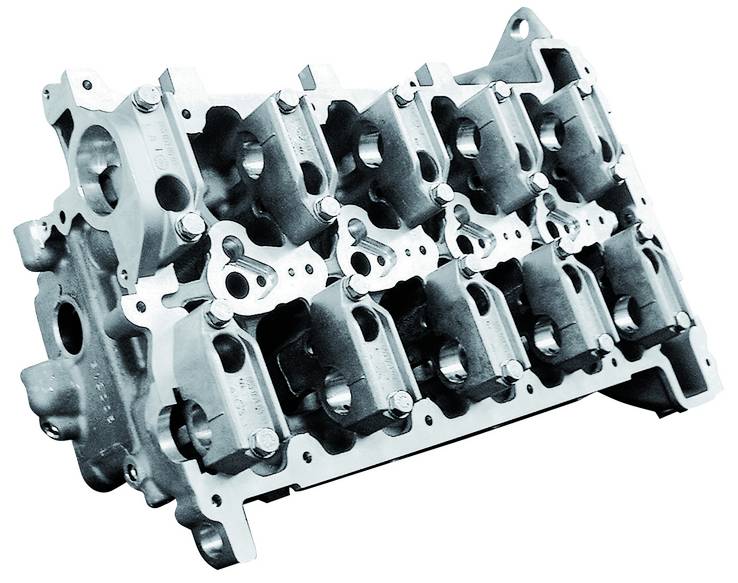
The Krause & Mauser Gruppe designs, produces and assembles standardised and specialist machine tools for the machining of workpieces across the whole automotive drive train from its sites in Oberndorf am Neckar and Vienna.
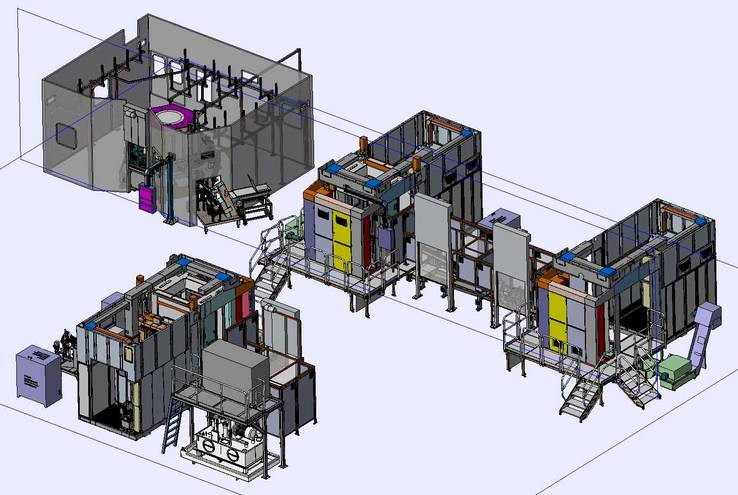
The modular concept has all the precision of specialist machines and allows increased production efficiency at the same time as reduced unit space.
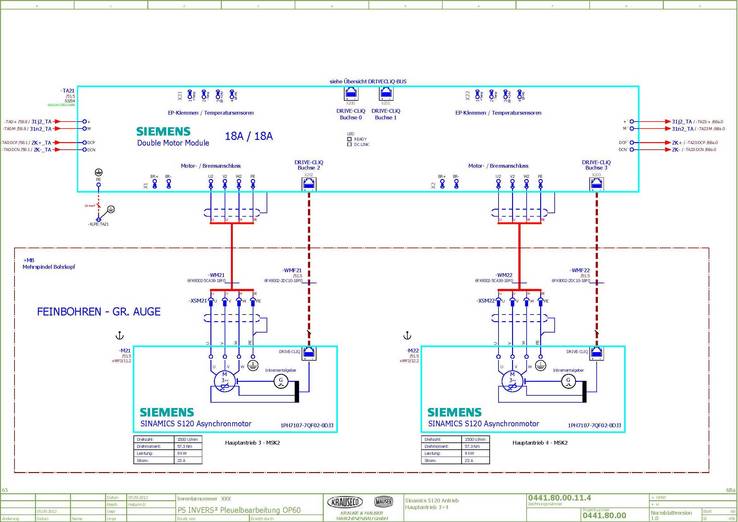
The electrical plans covering hundreds of pages have been produced using platform-based EPLAN Electric P8 since 2000.