Digitised representation of a wind turbine
Control cabinet design and wire harness assembly at Nordex
Can the length of a wire harness routed in a 120-meter wind turbine tower and connected directly to a control cabinet in a nacelle be precisely determined by a computer? Yes it can. Nordex, the fifth largest wind turbine manufacturer in the world, uses the EPLAN Platform extensively and in detail, and not just for wire processing and wire harness engineering.
Wind turbines alone in Germany produce around 50 GW of output and turbines from the Nordex Group are playing a significant role here. The company has been active in this fast-growing market since 1985 and is among the five largest manufacturers of wind turbines worldwide. In April 2016, Nordex merged with the wind energy division of the Spanish Acciona Group. The newly created group currently employs more than 4,800 people worldwide, achieved sales of around €3.4 billion in 2016, and has so far installed plants with an output of 21 GW.
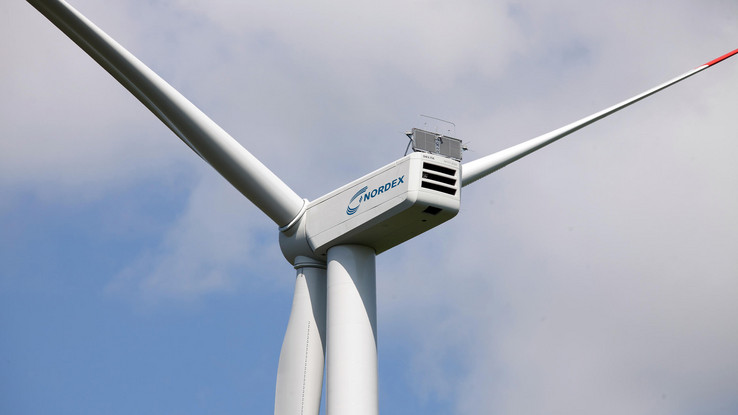
Up to 500 sensors are installed in a single wind turbine. Cabling is therefore becoming increasingly complex.
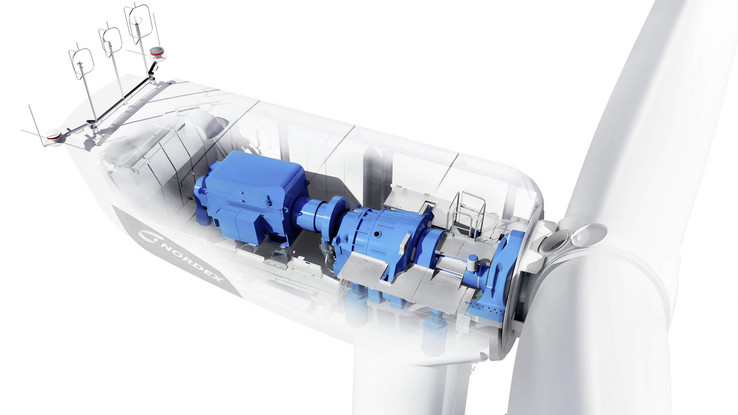
Not much space in the nacelle housing – and none at all in the middle. The wire harnesses to the eight decentralised control cabinets are therefore routed on the rounded nacelle walls.
A platform strategy with a diversity of options
Nordex offers its customers two turbine families: the Nordex product range, which is primarily used in Europe; and the Acciona Windpower turbine range which is in demand beyond Europe. In its core European market, Nordex focuses on the onshore 2.4–4.5 MW volume segment. In each power range, customers get Nordex turbines optimally adapted to wind conditions. Options are available for low, medium and high wind speeds, different tower heights and rotor diameters, anti-icing systems, condition monitoring and performance-enhancing features. Dr. Klaus Faltin, Head of Electrical Drives & Design at Nordex: “We offer 15 to 20 options for each series. Then there are the differing regional requirements, e.g. for grid connection.”
Modern line production – also for control cabinets
The individual series are built in quantities of several thousand. Nordex is thus a classic series producer and converted its main production sites in Rostock to ultra-modern line production at an early stage. Nacelle housings and rotor blades are manufactured there as well as control cabinets with around 100 personnel being involved in the task.
In five lines, up to 30 cabinets each move from station to station on skids, gradually being completed in large quantities. Wolfgang Conrad, Expert Engineer: “In addition to a centre box, seven decentralised cabinets and control boxes for individual functions such as yaw, azimuth and pitch drives are installed in each nacelle housing”. Rittal cabinets are used here. The central control cabinet in the nacelle consists, for example, of two TS8 control cabinets from the proven Rittal system series as well as equipment from other well-known manufacturers.
“We want to get the most out of EPLAN”
Nordex uses the EPLAN Platform and they have a clearly defined goal: The electrical designers in Rostock are endeavouring to standardise the development as far as possible and to map every detail, however small, within the EPLAN Platform. Wolfgang Conrad: “Our goal is to get the most from EPLAN and to exploit the opportunities of standardised development and production as much as possible”. This is apparent already from the extremely high quality and detail of the bills of material and circuit diagrams. All components used, down to small and very small parts such as screws, nuts and washers, are acquired and automatically assigned to projects. The benefit is that any actual inconsistencies are detected immediately: “If a part remains unassigned or has no location, it gets noticed immediately due to all components being logically linked”.
This also applies to the sheet metal processing required for the control cabinets. Development Engineer Enrico Durka: “Previously, production personnel used templates for the drilling patterns in Rittal control cabinets. Now we generate a drilling pattern from EPLAN Pro Panel and send it as a DXF file straight to the processing machine”. This results in (internal) delivery times for drilled control cabinets being reduced from several weeks to times ranging from 48 hours to a maximum of one week.
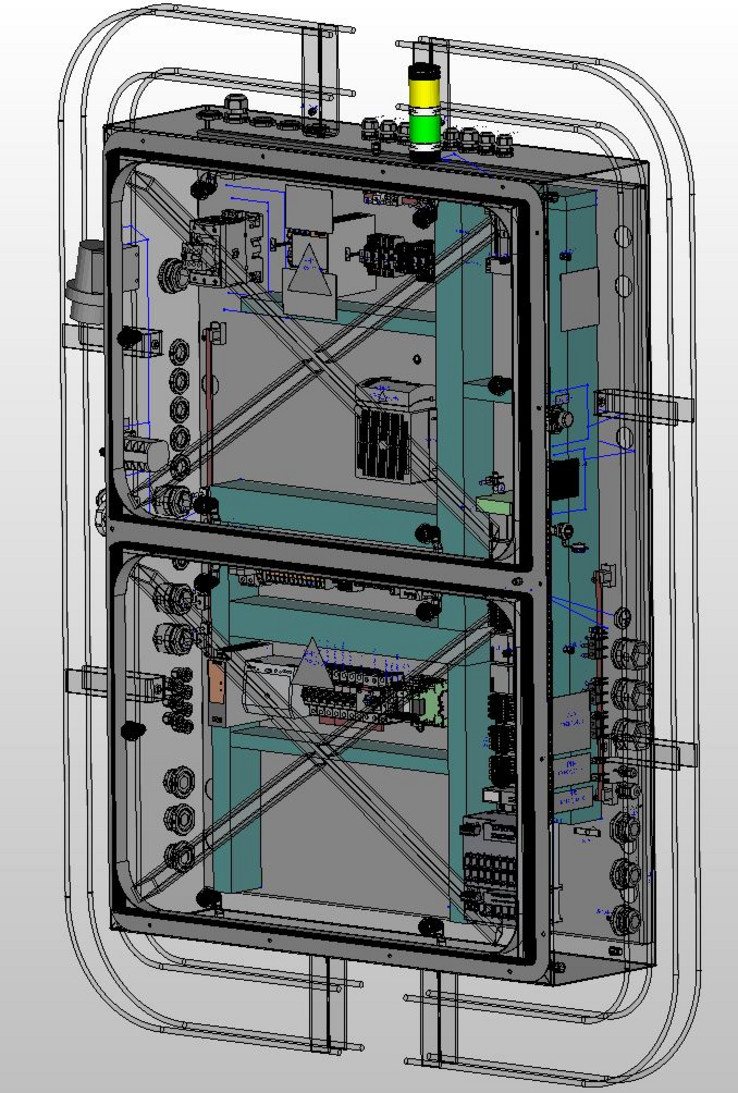
Hub control cabinet designed using EPLAN Pro Panel.
EPLAN Pro Panel: 3D routing with automated wire assembly
Nordex electrical designers also make intensive use of EPLAN Pro Panel in conjunction with EPLAN Smart Wiring. The basis here is data from 3D mounting layouts and connection information from circuit diagrams. One benefit resulting from this approach is wire-length determination using precision 3D routing. An electronic data record is then generated and sent to the external wire assembler. Wolfgang Conrad: “We design new control cabinets using only EPLAN Pro Panel and the Smart Wiring module. They enable extremely high standards of quality – and you also have to remember that they also need to produce highly precise work”.
Cable routing in towers and nacelles using EPLAN Harness proD
The positive experience gained from using EPLAN Pro Panel has led to Nordex taking a second step of wire harness engineering, i.e. cable routing in a 3D model to the tower, and from the control cabinets to consumers. This is where EPLAN Harness proD comes into play, and Nordex is using it very intensively. Martin Richter, responsible for wire harness design: “The drive train is located in the nacelle’s middle, so the wire harnesses are routed on the inner rounded panels. It is therefore extremely challenging to determine lengths”. Each cable is specified according to 16 parameters. These include source/sink, control points and bend radii. Even the position of cable ties and earthing straps is precisely defined. “As a result, we benefit from all wire lengths, connector variants, labelling etc. now being clear and consistent”.
Always fits: “All-inclusive” routing
During implementation of EPLAN Harness proD, electrical designers put samples to the test and made a comparison between “humans” and “machines”. Martin Richter: “The task was to measure the nacelle housing of a prototype and determine the lengths of 50 cables running along the panels. Two employees in production needed one day to determine exact measurements. Using EPLAN Harness proD, this amount of effort wasn’t required and we needed just a third of the time for the task”. This positive result was reaffirmed in a very similar test for a tower wire harness: “Here, 27 individual lines of cabling at a length of around 120 metres per phase required routing. Any miscalculations were in the low centimetre range. Routing tracks always fit precisely and we don't need to plan for extra cabling even for very long cables”. Based on this experience, Nordex designers have started to route cable ducts in the tower as source-target wiring right into the control cabinets.
Goal: Digital representation of a complete turbine
With the EPLAN Platform, Nordex's electrical designers are getting closer to their goal of digitizing the entire wind turbine. Dr. Klaus Faltin: “When we have a ‘digital mock-up’ of the system in the computer, we can act without a real prototype for design purposes and directly produce an initial example for production”. This is desirable because systems are becoming increasingly complex. Today, more than 500 sensors are already being installed in a single system and the trend continues to rise.
In any event, EPLAN data as a detailed basis is already available. Wolfgang Conrad: “We work with very large data models from 9 to 11 GB”. Nordex also maintains a comprehensive database of the components used. This includes 3D data models from the EPLAN Data Portal which is undergoing continuous growth and enhancement. Data generated in EPLAN is also to be used beyond design purposes. Dr. Klaus Faltin: “In future, we will work with the EPLAN Viewer even more intensively, e.g. directly at the production line, and we are currently carrying out a test phase”.