Deep-level integration
With more than 5,000 employees and a turnover of 1.5 million Swiss Francs, the "Textile Systems" division of Rieter AG is one of the leading companies in the field of textile system manufacturers.
With more than 5,000 employees and a turnover of 1.5 million Swiss Francs, the "Textile Systems" division of Rieter AG is one of the leading companies in the field of textile system manufacturers. The machines process natural and man-made fibers as well as their blends to yarns. A unique selling proposition for Rieter is that it can provide complete processing lines for the textile industry, from the cotton to the final yarn. These lines integrate, for example, the processing steps of cleaning, carding, drawing, combing, and ring or rotor spinning. A more recent and fast-growing business segment is that of nonwovens for which Rieter Textile Systems also provides overall solutions. With 21 production sites in eleven nations, the group of companies is represented worldwide. It is thus not surprising that the larger part of the turnover – about 70% - is made on the Asian markets. World records in textile machine manufacturing
Rieter Textile Systems is strongly technology-driven. During the past ITMA, the most important fair in this branch, Rieter machines set a total of four world records – for example with the most powerful carding system and the longest ro-tor spinning machine with 500 spinning positions and up to four autonomous ro-bots. Designing plays a correspondingly large role and is located at five sites. In addition to the headquarters in Winterthur (Switzerland), these are Ingolstadt (Germany) (for the rotor and draw frame product ranges), Ústí nad Orlicí (Czech Republic), Pune (India) and Czangzhou (China). Starting basis: Heterogeneous CAD landscape
Due to acquisitions in the past years, the designers at the various sites origi-nally had to work with different design tools. However, cooperation on the opera-tive level is close, as shown by an example: The draw frame machine RSB-D 40 that draws the yarn before it is spun into fibers, thus creating an important prereq-uisite for quality, has been built more than 25,000 times within a brief period and has been mounted in more than 100 countries. It was developed in Ingolstadt, but the production and final assembly were carried out in the Czech Republic and China in addition to Ingolstadt. The teams in the three countries cooperate across locations and, with EPLAN Electric P8, can access the same basic data. Benchmark: Search for uniform CAE system
"Collaborative engineering" is thus required. It is only logical to strive for standardization of the CAx tools. Christian Häringer, responsible in the Rieter headquarters in Winterthur for the standardization of the E-CAD systems: "If one wants to cooperate closely and also standardize components, using the same tools is an absolute must." Therefore, the decision to carry out benchmarking in order to find the optimal CAE system was taken in 2005. In a direct comparison of the systems, EPLAN Electric P8, which had just been launched in 2006, prevailed and was introduced directly at all the design locations. The responsible persons regarded it, amongst others, as a great advantage that no additional scripts are re-quired. Documentation in 15 languages, five languages for development
A further advantage that speaks for the use of EPLAN is its availability worldwide and the possibility of using many languages. The Rieter electrical de-signers do their design work in five languages (German, Czech, French and Chi-nese, each in combination with English), and the documentation can be made available to the international customers in fifteen languages. Free selection of the languages
For these tasks Rieter uses a central EPLAN language module in which all the relevant terms and translations are administered. Practically this means: The EPLAN projects are stored independently of the language. As soon as the user requests or edits a document, it is displayed in the desired output language. And if the documentation is required afterwards in a different language, because, for ex-ample, the machine was developed in the Czech Republic, but will be installed in France or India, the set of documents can be generated automatically: A consider-able facilitation in work for a company that is as present internationally as Rieter is. Communication between ERP and E-CAD per XML
Rieter also created a solution for communication between SAP R/3 as the ERP system and EPLAN, thus facilitating work. The two systems exchange data in XML format. This ensures a high degree of transparency. For example, the Pur-chasing department or the Sales department can open the EPLAN documentation of individual systems in SAP. Although SAP is the leading system, the EPLAN specific data are, however, maintained in EPLAN. And the SAP and EPLAN data are naturally synchronized automatically. The fact that large volumes of data are involved is illustrated alone by the fact that about 70,000 parts are stored in the EPLAN files. The M-CAD system Unigraphics NX is also linked to SAP through the same interface. By the way, the interfaces that allow this communication were adapted by the IT specialists of Rieter to the requirements of their colleagues. Since they believe it to be important that the know-how for IT procedures is kept in the company instead of being delegated. And as far as possible to do without additional mod-ules, such as separate interface tools, that involve further work for maintenance and updating. This also applies for the tools that allow working across locations: The "Collaborative engineering" tool is often used, authorization management is carried out professionally via SAP. Mechatronics: E-CAD and M-CAD with the same look-and-feel
A central topic which the Rieter engineers at all locations will have to deal with in future is mechatronics: The extremely powerful and rapid textile machines – the rotor spinning machines run at an unbelievable 160,000 revolutions per minute – are increasingly made of modules in which mechanical and electrical components are combined into functional units. In a first step Rieter is therefore striving to an identical look-and-feel of EPLAN Electric P8 and the M-CAD sys-tem Unigraphics. This is achieved by means of the DSC interface (Drive Solution Catalogue) that also facilitates variant design considerably: Individual machine types are available with up to 500 options. The trend towards mechatronics was, by the way, a further reason for Rieter to opt for the new CAE generation in 2006: This offered the option of also inte-grating the fluid power design through EPLAN Fluid. Thanks to the EPLAN plat-form on which both systems are based, electrical engineering and fluid power now use the same data basis. Direct coupling to SAP
The excellently integrated infrastructure required an exact migration to EPLAN Electric P8. There are power users at the individual locations whose data have already been migrated successfully. The employees at the various design location were trained step-by-step. This is not a small task by any means. After all, in the final version 60 employees will be working with 40 licenses worldwide. Goal: Uninterrupted design
To this purpose Rieter uses a self-developed tool for importing updates and patches. The tool is characterized by the fact that a fallback level is always avail-able during tests by the power users: If an error occurs, the central IT in Winter-thur can return to the old version without any data loss and without impairing the work of the designers. Not until the power users approve the system, is it installed at all the authorized workplaces. Meaning that the user is always on the safe side and can work without any interruptions: An important goal for a company that is as technology-driven as Rieter Textile Systems.
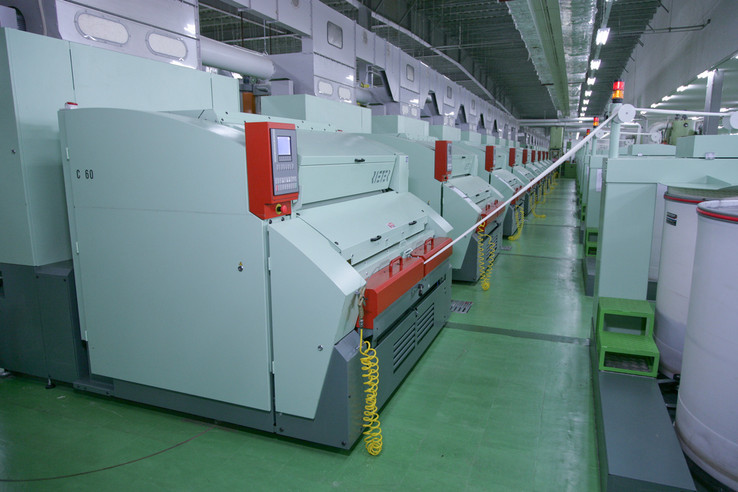
Complete installations from Rieter provide more than only spinning machines from the fiber to the yarn. Perfect matching of the machines throughout the entire process ensures economical manufacturing of the required yarn quality.
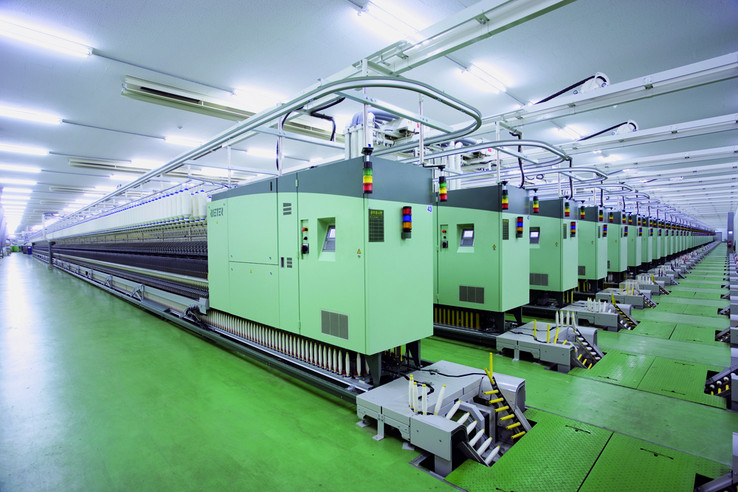
High-grade quality yarns are produced extremely economically – the example shows the ring spinning machine G 35 that is characterized by its modular struc-ture and the flexible number of spindles up to a maximum of 1632 spindles.