350,000 records available now around the world
As part of the RiPrio project, Rittal is currently introducing a consistent configuration solution based on the EPLAN Engineering Center (EEC) from its sister company EPLAN.
The April issue of the CAD-CAM REPORT reported on the RiPrio project in which Rittal is building up a consistent configuration solution for its enclosures, flow divider systems and IT infrastructure products. The configuration described based on the EPLAN Engineering Center requires a consistent CAD and, more importantly, PDM environment to produce all documents necessary for the planned variants within an order on a fully automated basis. This second instalment of the article on the RiPro project describes the consolidation of the CAD and PDM environment with the support of sister company EPLAN. It is no simple task, as there are over 350,000 technical records to maintain in order to ensure the most up-to-date version is always available around the world. As part of the RiPrio project, Rittal is currently introducing a consistent configuration solution based on the EPLAN Engineering Center (EEC) from its sister company EPLAN (see CAD-CAM REPORT 4/2012, p. 28). While the production control knowledge for the entire product range of the Herborn-based company is gradually reflected in the EEC, the production control knowledge continues to be managed within the SAP configuration solution. In order to provide the technical data required for the product description and for production, Rittal installed Autodesk's PDM solution Vault professional for around 500 users across the company. Production sites including Italy and the USA were included in what EPLAN believes to be the biggest Vault roll-out in Europe. "We are talking about over 350,000 technical records - mainly 3D models, 2D drawings and bills of materials - which we need to manage," explains Bernd Lehnert, R&D department manager at Rittal in Herborn and responsible for technology and support. "This requires a PDM solution as a consistent information and management basis for all technical product data." In the future, once the product know-how is stored in the EEC, Rittal can configure its products efficiently and process orders on a largely automated basis. "Our aim is to generate all technical order data automatically," Lehnert goes on. "Initially, this goes through the EEC - the heart of the configuration logic - but, of course, the PDM system needs to supply the basic data." This includes bills of materials and work plans, as well as CAD and NC data for production. The same applies to the optional fitting of accessories, including more than 5,000 parts - and it is in this area in particular that the aim is to make choosing the correct equipment as easy as possible for customers in future. "This should reduce the manual effort involved in order processing by means of the number of variants approved." In concrete terms, what this means can be seen based on the compact type AE enclosure, the logic of which is already entered in the EEC. As a series product, the enclosures can be configured not only with respect to the equipment, including mounting of accessories if required, but also with respect to raw processing and customer-specific finishes. If a customer does not want to make their own openings - for fans or buttons, for example - Rittal can do it for them on an individual basis. Not only are these easier to do in the raw component, there are also advantages with respect to corrosion protection as the paintwork is only applied afterwards. "It is also decisive that we want to avoid manual labour in this process," emphasises the head of R&D. "CAD model, drawings, bills of materials, work plan, calculation and NC data are all generated automatically - leading to significantly more efficient processes." In the future, it will be possible to generate drawings for production and quality control containing the important dimensions completely automatically. The accessories to be fitted can then be clearly assigned to the relevant openings. IT integration as a challenge
When implementing the strategy of the RiPrio project, the most important thing is the integration of the IT systems. "EEC, CAD, PDM and ERP need to be networked together, especially as we want to generate CAD drawings automatically - so we need to make sure that the basic technical data is available from a CAD perspective," Bernd Lehnert continues. "Enabling this interaction is a real challenge, as the definition of the specifications document was complex enough." The background is that Rittal is optimising its entire organisation as part of the RiPrio project, which means checking all workflows in advance and modifying where necessary - with the associated impact on the structure of the company, including the qualification of the employees. There was also plenty to do from a CAD perspective, as there was no standard system in the company before the start of 2000. This primarily involved using Autodesk's AutoCAD, as the 2D editing was mainly sufficient for the various sheet metal parts. Autodesk Inventor, Catia and Pro/Engineer were also used - especially for the more complex products such as IT racks with air-conditioning. "The result was a very assorted system environment for us," Lehnert remembers." "We therefore decided to use the Autodesk products Inventor and AutoCAD as standard." They offer the Rittal designers all the functions they need relative to the product range, so that they can achieve good value for money, among other things. Currently, the data for all current catalogue products is being standardised in Inventor, while other systems are only retained for OEM customers and old data, in case any changes are required. "At this point, the CAD manufacturers still have work to do to make sure that complete 3D models can be exchanged within the entire hierarchy - the systems are still relatively closed worlds," reports the R&D head. Although a lot of data can be exchanged through neutral formats such as STEP, information is often lost, especially hierarchy-related data in more complex models. CAD and PDM closely linked
Opting for the Autodesk products also meant deciding in advance on the PDM system. "This always requires a good interface to the CAD solutions in the company in order to achieve a high level of acceptance and thus becomes relevant," explains Bernd Lehnert. "That means: without a sensible interface and sensible control workflows, the systems will not be accepted." The CAD system needs automatic access to the database and to check the data in again before powering down - this integration is important. "With solutions from third-party providers, this often requires additional work to adapt interfaces and implement our own requirements - especially when updating a system component," explains the IT professional. It was beneficial to Rittal that its sister company EPLAN, which was already involved in RiPrio via the installation of the EEC, has consultancy know-how and can provide services relating to Vault and Inventor. "Because the Rittal product range has been growing over many years, there was no IT solution on the market which fitted 100 percent with our requirements - so we needed customer-specific adjustments at this point," clarifies Lehnert. This allows functional extensions and upgrades. For example, the NC data is saved within the product to allow the NC programmer to work efficiently. "This all increases user-friendliness and therefore acceptance." EPLAN was also involved in migrating the old data. The plan was to import the 350,000-plus records into the new PDM solution with the highest level of automation possible. But the first stage was to standardise the data from a range of different CAD solutions - including different versions of the same system. "Preparing the CAD data was very time-consuming, as the old data was not necessarily included in every move to a new release - because there is no added value in that by itself," reports Bernd Lehnert. "In the migration to Inventor, it often became clear that the existing models are not consistent and, for example, missing references in the models need to be created as part of the migration process - which means a lot of work for the developers." As a result, through Vault Professional and Inventor, Rittal will now have access to a development platform which can not only be perfectly controlled from the EPLAN Engineering Center, but also allows good networking of the international development and production sites. Although the majority of the products are developed in Herborn, they are produced in various locations around the world. "The aim is to achieve a single data source so that all technical data is available in its most up-to-date form at all times," Bernd Lehnert concludes. Although the PDM system data is mirrored across the locations, Vault brings the mechanisms for automatic data reconciliation with it "This means that only the data for special country-specific products is stored at a local level." Author: Michael Corban, PLM IT REPORT, published in PLM IT Report / 1/12 / November 2012
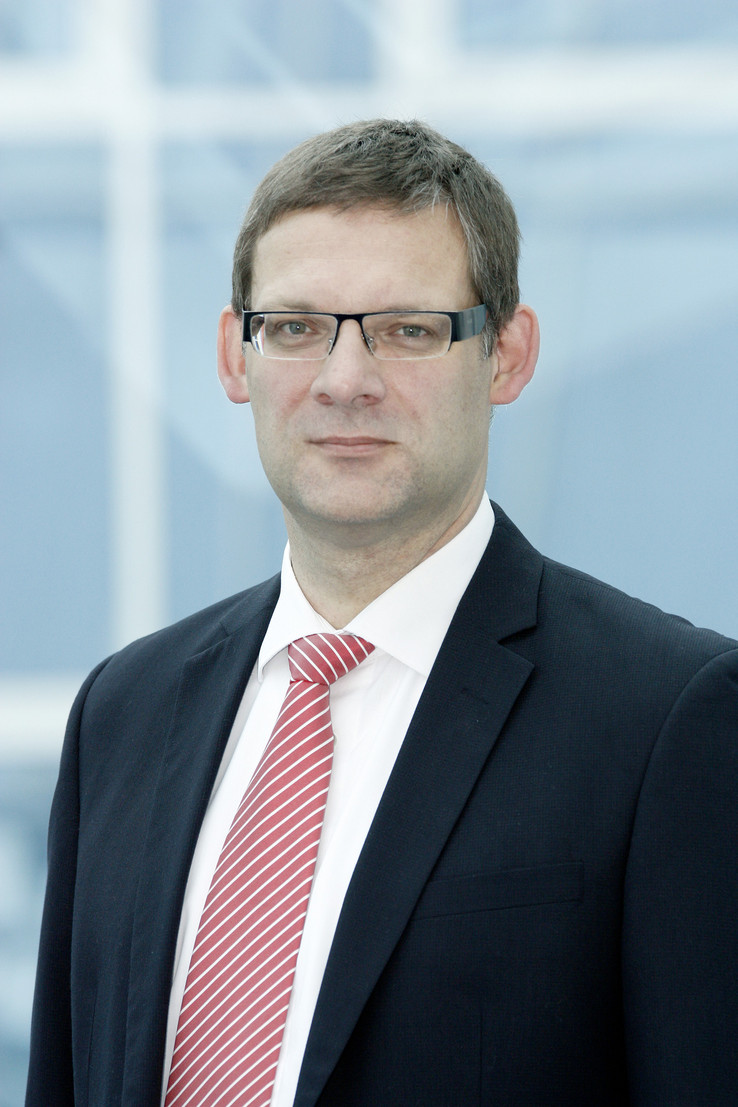
We use the PDM as a database from product development through change and revision management to product discontinuation," explains Bernd Lehnert, R&D Product Manager at Rittal in Herborn and responsible for technology and support.